The manufacturing industry has evolved from manual craftsmanship in ancient times to the mechanized production of the Industrial Revolution, and further to the automation era of the 20th century. Despite these advancements, the industry has long faced complaints about inefficiencies, waste, high costs, and inconsistent quality. Workers also raised concerns about unsafe conditions and job displacement due to automation. The constant pursuit of innovation has driven the industry to seek solutions, culminating in today’s adoption of advanced technologies like AI.
Today, Generative AI is at the forefront of this evolution, bringing transformative changes to the industry. By leveraging algorithms that can generate designs, optimize processes, and predict outcomes, generative AI is revolutionizing how products are conceived and produced. In manufacturing, it enables the creation of complex, innovative designs that were previously impossible, while also streamlining production workflows. From reducing material waste to enhancing product quality, generative AI is not just a tool but a game-changer, driving the next wave of innovation and competitiveness in the manufacturing sector. The future of manufacturing is being shaped by these intelligent, adaptive technologies.
Enhancing Design Accuracy with AI-Driven Modeling
AI-driven modeling is revolutionizing design accuracy in the manufacturing industry, setting new standards that surpass traditional methods. Conventional design processes often involve extensive trial and error, which can be time-consuming and costly. In contrast, generative AI algorithms analyze vast datasets to create precise models, optimizing for factors such as material efficiency, durability, and cost. These algorithms can simulate thousands of design variations, ensuring that the final product is not only innovative but also meets exact specifications. This high level of precision reduces errors and minimizes the need for costly revisions, resulting in products that perform reliably in real-world conditions.
Moreover, AI-driven modeling enables rapid prototyping and testing, significantly speeding up the design process. Engineers can quickly visualize complex designs, make real-time adjustments, and refine models based on immediate feedback. This iterative process allows for faster development cycles, enabling manufacturers to bring products to market more quickly. Additionally, the ability to explore a wider range of design possibilities encourages innovation, allowing manufacturers to create cutting-edge products that were once thought to be unachievable. By enhancing accuracy, reducing costs, and fostering creativity, AI-driven modeling is transforming the landscape of manufacturing design, making it more efficient and effective than ever before.
Streamlining Production Processes with Predictive Analytics
Streamlining production processes through predictive analytics represents a major leap in manufacturing efficiency. By harnessing data from various sources—such as real-time sensors, historical production records, and sophisticated machine learning algorithms—predictive analytics allows manufacturers to anticipate potential disruptions before they occur. This proactive approach means that maintenance can be performed before equipment failures happen, reducing unplanned downtime and ensuring smooth operations. As a result, overall production efficiency is significantly enhanced, with fewer interruptions and more consistent output.
In addition to optimizing maintenance, predictive analytics plays a crucial role in refining supply chain management. By delivering precise demand forecasts, it enables manufacturers to accurately align inventory levels with anticipated needs. This foresight helps in adjusting production schedules and managing stock more effectively, minimizing the risks of both overstocking and shortages. Consequently, manufacturers benefit from a more responsive and flexible production system that not only reduces costs but also boosts customer satisfaction. Embracing predictive analytics allows manufacturers to improve operational efficiency, cut waste, and maintain a competitive edge in a rapidly evolving industry.
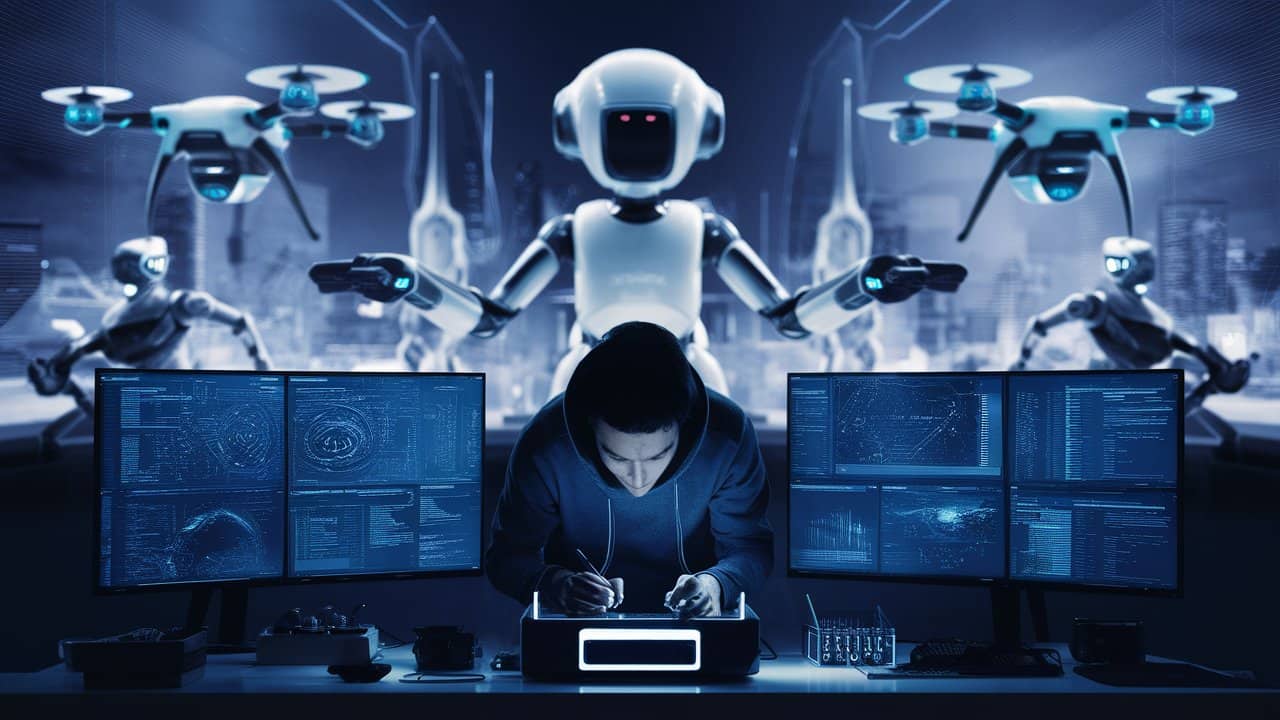
Quality Control Redefined: AI Inspection and Optimization
Quality control has always been a critical aspect of manufacturing, but traditional methods often struggle with inconsistencies and inefficiencies. The introduction of AI inspection and optimization represents a paradigm shift in how quality is maintained. AI-powered systems utilize advanced machine learning algorithms to inspect products with unprecedented accuracy. By analyzing images and sensor data, these systems can detect defects, deviations, and anomalies that might elude human inspectors. This not only enhances the precision of quality checks but also speeds up the inspection process, reducing the likelihood of costly recalls and ensuring higher standards of product excellence.
Moreover, AI-driven quality control systems can continuously learn and adapt over time. As they process more data, they refine their algorithms to improve detection capabilities and predict potential issues before they arise. This proactive approach enables manufacturers to address problems at their source, preventing defects from reaching the final stages of production. By integrating AI with existing quality control processes, companies can achieve a level of consistency and reliability that was previously unattainable.
The benefits of AI in quality control extend beyond mere detection. Optimization algorithms can analyze production data to identify trends and patterns that might indicate underlying issues. This data-driven insight allows manufacturers to fine-tune their processes, enhance operational efficiency, and minimize waste. As AI continues to evolve, its role in redefining quality control promises to drive innovation and set new benchmarks for excellence in manufacturing.
Benefits of AI in Manufacturing
Cost Reduction
The integration of AI into manufacturing processes heralds a new era of efficiency and cost-effectiveness. One of the most compelling advantages is cost reduction. Leveraging AI for predictive maintenance, optimizing resource allocation, and employing generative design techniques enables manufacturers to achieve substantial savings. Predictive maintenance algorithms, for instance, preemptively identify equipment issues, which minimizes downtime and costly repairs. Additionally, AI-driven resource optimization ensures that materials and energy are used efficiently, further cutting operational expenses.
Improved Product Quality
Another pivotal benefit is improved product quality. AI-powered quality control systems set a new standard for precision and consistency in manufacturing. These advanced systems detect even the slightest deviations or defects, ensuring that each product meets rigorous quality standards. By reducing human error and variability, AI enhances overall product reliability and customer satisfaction. Manufacturers can confidently deliver products that not only meet but exceed customer expectations, thereby bolstering their reputation in competitive markets.
Increased Productivity
Furthermore, AI enhances productivity through smart automation and streamlined processes. Automated systems powered by AI algorithms handle complex tasks with speed and accuracy, resulting in increased production output without compromising quality. By optimizing workflows and eliminating bottlenecks, manufacturers achieve higher throughput rates and quicker turnaround times. This not only boosts operational efficiency but also allows businesses to meet growing demand effectively. In essence, AI transforms manufacturing into a more agile and responsive industry, capable of adapting swiftly to market dynamics while maintaining high standards of productivity and quality.